Hydraulic Tube Fittings Manufacturer: Revolutionizing the Industry with Quality
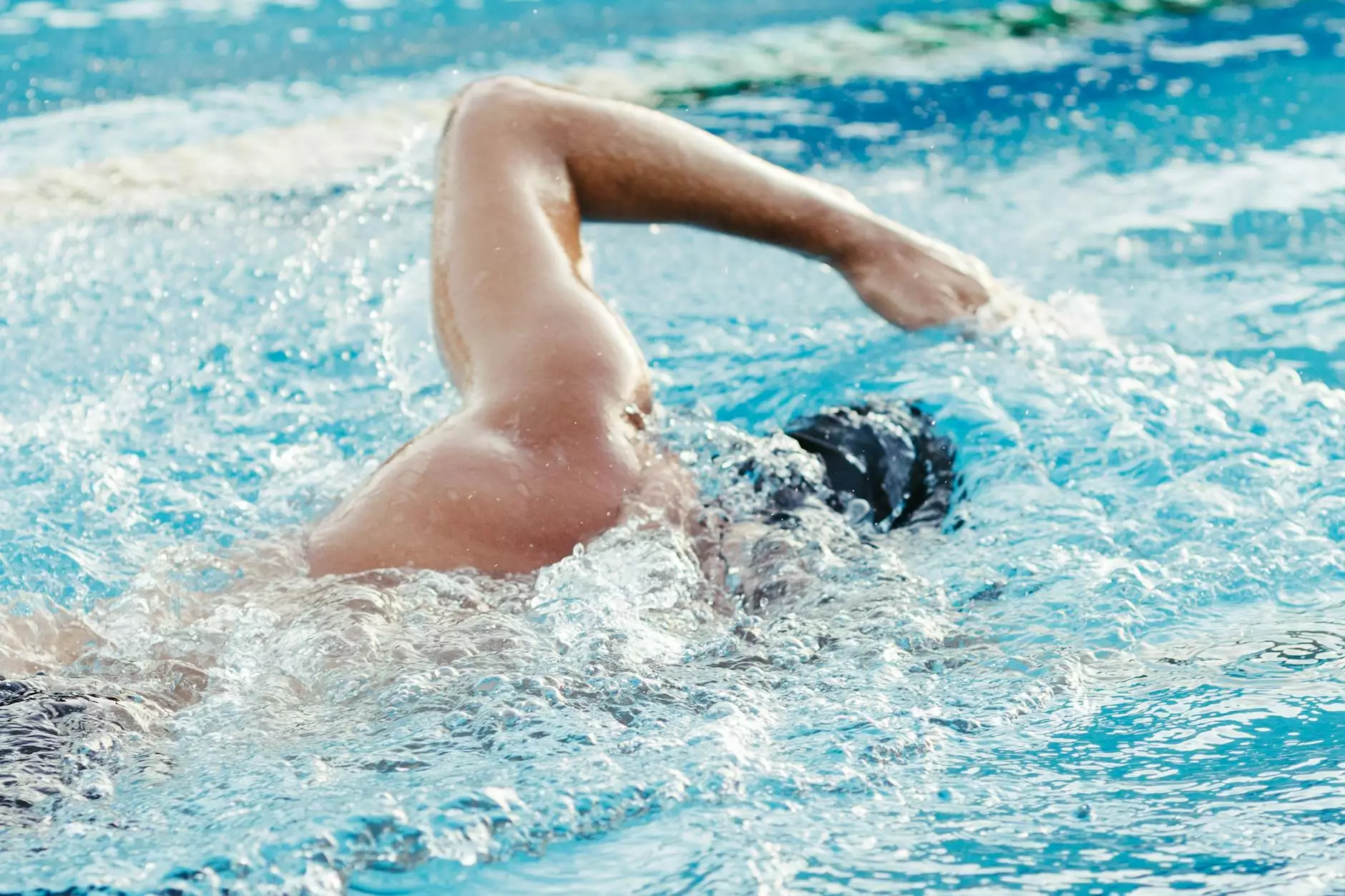
In today's fast-paced industrial world, the role of a reliable hydraulic tube fittings manufacturer cannot be overstated. Manufacturers like Fitsch provide essential components that ensure the efficiency, safety, and durability of hydraulic systems. Understanding the dynamics of hydraulic systems and the critical role fittings play can be the key to achieving optimal operational performance in various applications.
What Are Hydraulic Tube Fittings?
Hydraulic tube fittings are connectors used to join various components within hydraulic systems. These fittings facilitate the transfer of fluids under pressure and are integral to the overall functionality of machinery used in construction, manufacturing, and automotive fields. High-quality fittings must withstand extreme temperatures and pressures while maintaining leak-proof integrity.
Types of Hydraulic Tube Fittings
Hydraulic fittings come in several types, each designed for specific applications:
- Compression Fittings: These fittings are used to connect two tubes together. They compress onto the tube when tightened, ensuring a secure fit.
- Flared Fittings: Flared fittings are distinct in their design. They consist of a flared end that creates a wider surface area for better hydraulic sealages.
- Threaded Fittings: Threaded hydraulic fittings are used to join pipes and tubes together through threaded connections. They come in various thread standards.
- Quick Disconnect Fittings: These allow for easy connection and disconnection without the need for tools, making them ideal for service equipment.
- Pipe Fittings: Pipe fittings are utilized to change the direction or flow of hydraulic fluids in addition to connecting tubes.
Why Choose Fitsch as Your Hydraulic Tube Fittings Manufacturer?
Choosing the right manufacturer for hydraulic tube fittings is crucial to the success of your operations. Here’s why Fitsch stands out in the industry:
1. Quality Assurance
At Fitsch, we prioritize quality with every hydraulic tube fitting we produce. Our rigorous quality control processes, aligned with international standards, ensure that each product is durable, reliable, and designed to perform under high stress and temperature conditions.
2. Comprehensive Product Range
Fitsch offers an extensive range of fittings for sale, catering to diverse applications. Whether you need compression fittings, flared fittings, or any other type, our product line has you covered.
3. Innovation and Technology
As a leading hydraulic tube fittings manufacturer, we embrace modern technology in our production processes. This commitment to innovation helps us develop advanced fittings that meet the evolving demands of various industries.
4. Expert Engineering Support
Our team comprises highly skilled engineers and technicians who are always ready to assist customers in selecting the correct fittings for specific requirements. Their expertise can help streamline your projects and save time and costs.
Applications of Hydraulic Tube Fittings
Hydraulic tube fittings are applied across many industries. Below are some of the primary sectors that rely heavily on these components:
- Construction: Hydraulic systems in construction equipment like bulldozers, excavators, and cranes rely on high-quality fittings to maintain fluid transfer.
- Manufacturing: Production lines utilize hydraulic machinery, and secure fittings assure uninterrupted operation.
- Aerospace: In aviation, hydraulic systems control everything from landing gear to wing flaps; reliable fittings are crucial for safety.
- Automotive: Hydraulic tube fittings are used in brake systems and power steering, making them essential for vehicle safety and performance.
- Marine: Hydraulic systems in marine applications require corrosion-resistant fittings designed to withstand harsh environmental conditions.
Understanding the Manufacturing Process
Behind every high-quality hydraulic tube fitting is a complex manufacturing process that ensures precision and reliability. Here’s a brief overview:
1. Material Selection
The first step in manufacturing dependable hydraulic fittings is choosing the right materials. Common materials include:
- Stainless Steel: Known for its high strength and corrosion resistance.
- Brass: Excellent for low-pressure applications due to its corrosion resistance and machinability.
- Carbon Steel: Offers superior strength, making it ideal for high-pressure fittings and applications.
2. Machining and Forming
Once materials are selected, the manufacturing process involves various machining and forming techniques, including:
- CNC Machining: Computer Numerical Control (CNC) machines are used to create precise fittings.
- Stamping: Metal stamping techniques are used for mass production of fittings and components.
- Forging: This process enhances the strength of the fittings and their resistance to fatigue and wear.
3. Surface Treatment
To improve performance and longevity, hydraulic fittings often undergo surface treatments, such as:
- Galvanization: Adds a protective zinc coating to prevent rust.
- PVD Coating: Physical Vapor Deposition improves the durability and aesthetic of fittings.
4. Quality Control
Before the fittings reach customers, they undergo rigorous testing to ensure they meet all specifications and standards. This includes pressure testing, dimensional inspections, and surface finish evaluations.
Choosing the Right Hydraulic Fittings for Your Needs
Selecting the appropriate hydraulic fittings involves consideration of several factors.
1. Pressure Ratings
Each hydraulic fitting has a specified pressure rating. It's essential to choose fittings that can withstand the pressures within your system.
2. Fluid Compatibility
Ensure that the materials of the fittings are compatible with the fluids used in your hydraulic systems to prevent corrosion or damage.
3. Temperature Range
Fittings must be chosen based on the temperature range of the hydraulic fluid, ensuring they remain functional without failing under stress.
4. Application Requirements
Identify the specific application the fittings will be used for and choose accordingly, considering factors like space limitations and required movement.
Future Trends in Hydraulic Fitting Manufacturing
The future of hydraulic fittings is being shaped by several transformative trends:
1. Sustainability
The construction industry is shifting towards sustainability, with manufacturers adopting eco-friendly practices and materials in production.
2. Automation and Smart Manufacturing
With advancements in Industry 4.0, automation in the production of hydraulic fittings is on the rise, enabling greater precision and efficiency.
3. Expanded Applications
The usage of hydraulic tube fittings is constantly expanding into new sectors, including renewable energy, automotive technologies, and robotics.
Conclusion
In the realm of industrial applications, hydraulic tube fittings serve as the unsung heroes that ensure smooth operations across various machinery and systems. By choosing a reputable manufacturer like Fitsch, businesses can secure high-quality fittings designed for durability, safety, and effectiveness. The right hydraulic fittings not only optimize performance but also enhance safety, promoting a productive work environment across all sectors. For your needs related to hydraulic tube fittings, consider Fitsch—a name synonymous with excellence and reliability in hydraulic solutions.