Injection Molding Automotive: A Comprehensive Guide
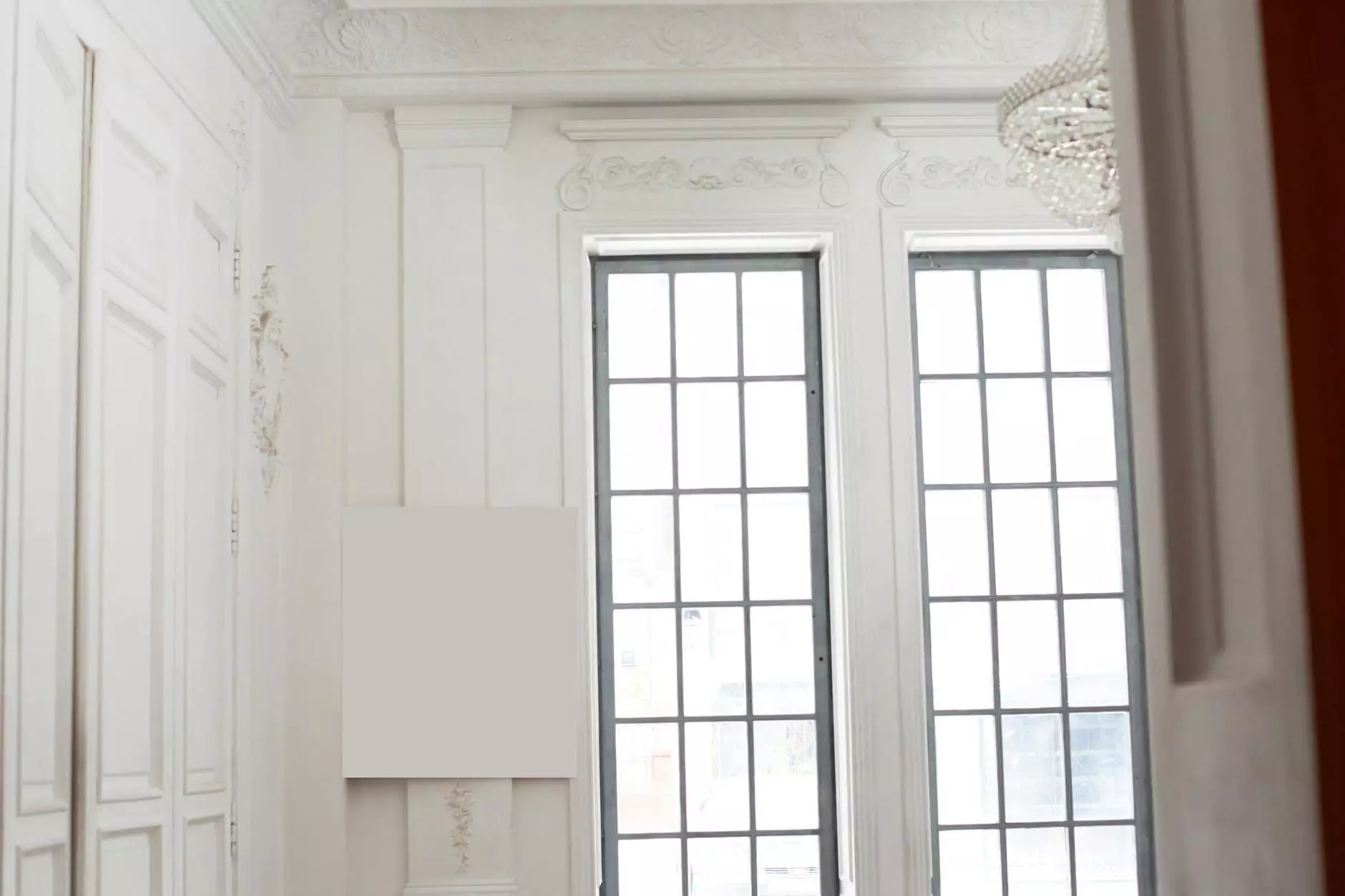
Injection molding automotive is a revolutionary manufacturing process that has transformed the way automotive parts are produced. This technique allows for the rapid production of complex components with high precision and consistent quality. In this article, we will delve into the intricacies of injection molding, its significance in the automotive industry, and how it integrates with metal fabrication, particularly through the expertise available at deepmould.net.
The Fundamentals of Injection Molding
At its core, injection molding involves the injection of molten materials into a rigid mold to create a solid part. This process is particularly suited for producing large volumes of identical parts, which is essential in the automotive sector where consistency and reliability are paramount.
How Does Injection Molding Work?
The injection molding process can be broken down into several key stages:
- Material Selection: The first step involves selecting the appropriate thermoplastic or thermosetting material that meets the specifications of the automotive part.
- Melting the Material: The selected material is heated until it reaches a molten state, ready for injection.
- Injection: The molten material is injected into a precisely designed mold, where it takes shape before it cools and solidifies.
- Cooling: The part is allowed to cool, solidifying into its final form.
- Demolding: Once cooled, the mold opens, and the finished part is ejected.
- Trimming and Finishing: Any excess material is removed, and the part may undergo secondary operations to meet the required specifications.
Advantages of Injection Molding in the Automotive Sector
The use of injection molding in the automotive industry offers a multitude of advantages:
- High Precision: Injection molding produces parts with tight tolerances, ensuring that components fit together perfectly in vehicles.
- Cost-Effective for High Volumes: Once the initial mold is created, the cost per unit for high-volume production is markedly low.
- Material Variety: A wide range of materials can be used, including various plastics and composites, allowing for innovation in part design.
- Reduce Waste: The process is highly efficient, minimizing waste and allowing for recycling of material.
- Complex Geometries: Injection molding can create intricate designs that would be difficult or impossible to achieve with traditional methods.
Injection Molding vs. Other Manufacturing Processes
When considering the manufacturing of automotive parts, several other methods exist, such as machining, die casting, and 3D printing. Each has its own benefits and drawbacks:
Machining
Machining involves removing material from a solid block to create a part. While highly accurate, it is often more time-consuming and generates more waste compared to injection molding.
Die Casting
Die casting is suitable for metals but often involves higher tooling costs and is limited to certain materials. It also doesn't provide the same level of flexibility in complex shapes as injection molding.
3D Printing
While 3D printing offers incredible design freedom, it typically falls short in production speed and cost-effectiveness when compared to injection molding for large runs.
The Role of Metal Fabricators in Injection Molding Automotive
Metal fabricators play a crucial role in the automotive industry, particularly when used in conjunction with injection molding processes. Their expertise contributes to:
- Mold Design and Fabrication: Skilled metal fabricators create the molds used in injection molding, ensuring precision and durability.
- Integration of Metal Parts: Many automotive components require the combination of plastic and metal. Metal fabricators can manufacture the necessary components that complement injection molded parts.
- Prototyping: Metal fabricators assist in rapid prototyping, enabling quick iterations and testing of designs before final production.
Case Studies: Successful Applications of Injection Molding in Automotive
Real-world examples illustrate the effectiveness of injection molding in automotive applications:
Case Study 1: Dashboard Components
One major automotive manufacturer utilized injection molding to produce intricate dashboard components. By designing the molds for multi-component assembly, they reduced the number of parts needed, minimized assembly time, and improved overall vehicle design aesthetics.
Case Study 2: Exterior Trim Parts
Another example involved the production of exterior trim parts for a new model. Injection molding allowed for unique shapes and finishes, providing not only functional benefits but also enhancing the visual appeal of the vehicle, which is important for market competitiveness.
Future Trends in Injection Molding and Automotive Manufacturing
The future of injection molding in the automotive industry is bright, with several trends set to shape the market:
Increased Use of Sustainable Materials
With a growing focus on sustainability, manufacturers are exploring bio-based and recycled materials for injection molding processes.
Advances in Technology
Innovations such as smart molding technology and automation will lead to more efficient production practices and reduced lead times.
Enhanced Design Capabilities
The integration of advanced simulation software allows for better analysis of mold flow and part design, pushing the boundaries of what can be achieved through injection molding.
Conclusion
Injection molding is not just a manufacturing process; it is a cornerstone of modern automotive production. As the industry evolves, the injection molding automotive process will continue to advance, benefiting from new technologies and material innovations. For businesses looking to excel in this arena, partnering with expert metal fabricators like deepmould.net can provide the necessary support to harness the full potential of this dynamic manufacturing process.
Call to Action
If you’re interested in learning more about how injection molding can optimize your automotive production, reach out to the experts at deepmould.net today. Our team is ready to assist in creating innovative, high-quality components tailored to your needs.